Objective of the intelligent analysis system used on the assembly line in its factory BMW Group in Regensburg is the prevention of unplanned interruptions in production. Predictive maintenance predicts and prevents – and that’s exactly what the intelligent monitoring system offers.
Data-driven analyzes of transport equipment enable early detection and prevention of potential breakdowns – thus maintaining an optimal flow in vehicle production.
The system supported by Artificial Intelligence (AI) annually prevents an average of around 500 minutes of downtime in vehicle assembly alone at the Regensburg plant.
For assembly at the Regensburg plant, vehicles are generally placed on mobile loading docks or chain-driven skid systems that pass through the production halls. Any technical error in the state-of-the-art conveyor systems can lead to a standstill in the assembly lines. This increases both maintenance and cost requirements. To prevent this, the factory’s innovation team developed a system that can detect potential technical problems early – and thus avoid any production losses. Affected parts of the transport element can be removed from the assembly line and repaired away from production.
The advantage is that the monitoring system does not require additional sensors or equipment, but evaluates the existing data from the installed components and the control system of the transport elements. If abnormalities are detected, an alarm sounds.
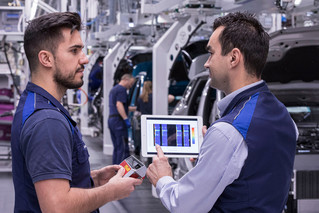
Source: News Beast
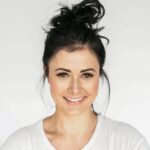
With 6 years of experience, I bring to the table captivating and informative writing in the world news category. My expertise covers a range of industries, including tourism, technology, forex and stocks. From brief social media posts to in-depth articles, I am dedicated to creating compelling content for various platforms.