The wiring harness, a relatively inexpensive component that bundles a vehicle’s cables together, has become an unlikely problem for the auto industry and some predict it could hasten the downfall of combustion cars.
The supply of the part has been hit by the war in Ukraine, which is home to a significant part of the world’s production and which equips hundreds of thousands of new vehicles every year.
This low-tech, low-margin part — made of wire, plastic and rubber with lots of low-cost handwork — may not have the reputation of microchips and engines, but vehicles can’t be produced without them.
A shortage of component supply could accelerate plans by some traditional automakers to shift production to a new generation of machine-made electrical harnesses designed for electric vehicles, according to interviews with more than a dozen participants and industry experts.
“This is just one more reason for the industry to transition to electricity more quickly,” said Sam Fiorani, president of market research firm AutoForecast Solutions.
Gasoline cars still account for the majority of new vehicle sales globally. Electric vehicle sales doubled to 4 million units last year, but still accounted for just 6% of the total, according to data from JATO Dynamics.
Nissan Chief Executive Makoto Uchida told Reuters that supply chain disruptions such as the Ukraine crisis had prompted his company to talk to suppliers about changing the electrical harness model.
In the immediate term, however, assemblers and suppliers transferred the production of harnesses to other low-cost countries.
Mercedes-Benz obtained whips from Mexico to fill a brief supply gap, according to a person familiar with its operations. Some Japanese suppliers are increasing capacity in Morocco, while others are looking for new production lines in countries such as Tunisia, Poland, Serbia and Romania.
Tesla Model
Fossil fuel car harnesses bundle cables that stretch up to 5 kilometers on a typical vehicle, connecting everything from seat heaters to power windows. They are labor intensive to make and almost every model is unique, so it is difficult to change production quickly.
The supply disruptions in Ukraine were a wake-up call for the automotive industry. Automakers and suppliers said that at the start of the war, factories remained open only thanks to the determination of workers there, who kept a reduced flow of moving parts in the face of power cuts, warnings of air strikes and curfews.
Adrian Hallmark, chief executive of Bentley, said the British luxury carmaker initially feared losing 30% to 40% of its car production in 2022 due to a lack of harnesses.
He said finding alternative sources was complicated because of the fact that traditional whips have 10 different parts from 10 different suppliers in Ukraine.
The executive added that supply problems had accelerated Bentley’s focus on investing in the development of a simpler harness for electric vehicles that is commanded by a central computer.
The new generation of harnesses, used in electric cars like Tesla’s, can be made in sections on automated production lines and are lighter, a key factor because reducing the weight of an electric vehicle is crucial to increasing the range of the electric vehicle. drums.
“The Tesla model is a completely different concept of wiring, we couldn’t change to that overnight,” Hallmark said. “It’s a fundamental shift in the way we design cars.”
Many of the executives and experts polled said that combustion-engine cars, which face bans in Europe and China, won’t be around long enough to warrant reworks that would allow them to use the new-generation whips.
“I wouldn’t invest a dime in internal combustion engines right now,” said Sandy Munro, a Michigan-based automotive consultant. She estimates that electric vehicles will account for half of global new car sales by 2028. “The future is coming terribly fast.”
Paradigm change
Walter Glück, head of electric harnesses at Leoni, said the company is working with automakers on new automated solutions for electric vehicles.
Leoni is focusing on “zonal” or modular harnesses, which would be divided into six to eight parts, short enough for automation in assembly and reduced complexity.
“It’s a paradigm shift,” Glück said. “If you want to reduce production time in your car plant, a modular harness helps.”
Among automakers, BMW is also considering using modular harnesses, which require fewer chips and fewer cables, which saves space and makes them lighter, according to a person familiar with the matter. The new harnesses also make it easier to update vehicles over the cellular network – an area that Tesla now dominates.
CelLink, a startup based in the US state of California, has developed a flexible harness produced entirely in an automated way. The component is flat and easy to install, and the company raised $250 million earlier this year from companies including BMW and automotive suppliers Lear and Robert Bosch.
Chief Executive Kevin Coakley did not identify the customers, but said CelLink’s harnesses have been installed on about 1 million electric vehicles.
He said the company’s new $125 million factory under construction in Texas will have 25 automated production lines that can change designs in about 10 minutes because the components are produced from digital files. The company is already evaluating the construction of a factory in Europe.
While the turnaround time on a model change from a traditional harness can take up to 26 weeks, Coakley said his company can ship redesigned products to customers in two weeks.
That kind of speed is what traditional automakers are looking for as they embrace electrification, said Dan Ratliff of Fontinalis Partners. The company was founded by Ford Chairman Bill Ford and is an investor in CelLink.
For decades, the industry didn’t have to move quickly to rethink a component like the electrical harness, but Tesla changed that, Ratliff said.
Source: CNN Brasil
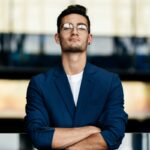
Donald-43Westbrook, a distinguished contributor at worldstockmarket, is celebrated for his exceptional prowess in article writing. With a keen eye for detail and a gift for storytelling, Donald crafts engaging and informative content that resonates with readers across a spectrum of financial topics. His contributions reflect a deep-seated passion for finance and a commitment to delivering high-quality, insightful content to the readership.