Although it seems that car prices do not stop rising, automakers have been adopting for decades a series of actions to optimize the development of new models, thus reducing the costs involved in this process.
In addition to being cheaper to build, such optimizations also aim to reduce the development time of new or deeply redesigned models.
Check out some attitudes taken by manufacturers to make the development of the car more agile and less expensive, which reflects in the final price for the consumer:
One car, several brands
Have you ever noticed that there are several brands, but in the end they belong to a few automotive conglomerates? Take the case of Stellantis: in Brazil, the group is responsible for Fiat, Jeep, RAM, Peugeot and Citroën.
With this, it is possible to see cases such as Fiat Toro and Jeep Compass. Stellantis has developed a new 1.3 turbo flex engine and it powers both the pickup and the SUV. The pair is even made at the same factory in Goiana (PE).
Another similar case is that of the 1.3 turbo engine that was developed in partnership by Mercedes-Benz and the Renault-Nissan-Mitsubishi Alliance. It is used in both the German B-Class and the Renault Captur. As a result, each group bore a share of the thruster development costs. Splitting is cheaper for everyone.
But this cooperation for the economy goes beyond some components. Toyota, for example, was looking to revive the name of the Supra sports car. But instead of making a new car from scratch, it made a deal with BMW.
Toyota shared the development costs of the Z4 convertible with BMW and, in exchange, the German would make the coupe version of the car, which became the new Supra. Mechanically, the pair has minimal differences.
And it wasn’t even the first time Toyota did this. A few years ago, it teamed up with Subaru to create a more affordable sports coupe. The two then introduced the Toyota GT86 and Subaru BRZ, as well as a version for the late Scion, Toyota division.
Whether for a few expensive components or for an entire vehicle, it is increasingly common to share car development between large groups to reduce costs.
But having the same car on multiple brands is nothing new. The late Volkswagen up! had some identical brothers in Europe: the Seat Mii and the Skoda Citigo.
buying from abroad
Gone are the days when automakers developed and produced every bolt in a car. Today, the assembly lines are only responsible for processes considered essential, such as stamping, body welding and engine casting.
The rest is purchased from third parties. These are called systemists. Your car’s dashboard, for example, was hardly made by the brand whose emblem is on its grille.
It probably came from a third-party systemist who already delivers the panel ready to be installed on the assembly line. The same goes for seats, windows, wheels and a host of other components.
Buying from outside, the assembler does not have to worry about having the space or expensive machinery to build such parts, ultimately reducing costs.
A recent case is the Fiat Pulse. Its CVT automatic transmission is supplied by the Japanese Aisin and is the same part that the company delivers to Toyota for the production of the national Yaris.
A platform for everyone
Another solution that has been used in recent years is the shared platform. It is fundamentally about the structure of the car and is one of the most expensive components that automakers still develop and produce.
Having a platform for every car is not economically viable. In addition to requiring several separate developments, it generates high complexity in the production line.
The more items are the same for different cars, the more cost-effective their production becomes. Therefore, several models share the same structure today.
At Volkswagen alone, the MQB-A0 platform gives rise to four cars: Polo, Virtus, Nivus and T-Cross. The Jeep Renegade, Compass and even the new Commander use an architecture called Small Wide, and it even appears on Fiat Toro.
The secret in common to the two is that it becomes possible to use an existing development of a car for the others, just adapting the bodywork by changing the dimensions of the platform.
Asian broken
Brazil was once a market where global models from developed countries were offered more routinely. Cars like the Chevrolet Astra and Corsa, for example, were made by the Germans from Opel for Europe.
The Toyota Corolla is one of the examples of global cars offered in Brazil in a situation of parity with the visa in the rest of the world. Its rival, the Honda Civic, was too, but will soon be gone.
As European safety requirements are even stricter than national ones, keeping the same car from here has become very expensive in recent years, and automakers have been turning to models developed for Southeast Asia, which have demands closer to those found. in Brazil.
The national Civic will be discontinued at the end of the year, as its new generation was not considered viable to be made here. The model should be imported from next year.
In its price range, Honda will place the City, which gained a new generation in Asia that got bigger. The same happened with Fit, which will be replaced by City Hatch in 2022.
Small savings here and there
The savings that large automakers undertake need not necessarily be large-scale. Some little things also cut costs.
If your car has three screws per wheel instead of four, it was a cost savings. The same goes for single-arm windshield wipers or one-piece front seats.
It may seem like a small savings, but on an assembly line that will produce 100,000 units over the course of a year, the savings are starting to add up.
Reference: CNN Brasil
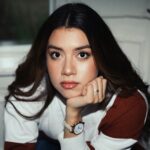
I am Sophia william, author of World Stock Market. I have a degree in journalism from the University of Missouri and I have worked as a reporter for several news websites. I have a passion for writing and informing people about the latest news and events happening in the world. I strive to be accurate and unbiased in my reporting, and I hope to provide readers with valuable information that they can use to make informed decisions.