A large multi-storey factory, with enormous cylindrical barrels in which the pigments are mixed and ribbons on which small precious parts slide which, once assembled, will become markers. We visited the Carioca factory in Settimo Torinese, 20 thousand square meters large, where we produce approximately 1.2 million markers per day.
In this factory – founded in 1956 by the entrepreneur Alessandro Frola and relaunched in 2016, after being acquired by a new company owned by Enrico Toledo’s family and a group of friends – the entire production cyclefrom the molding of components with plastic materials to the wrapping and packaging of the finished product.
In the plant, in addition to the molding and assembly departments, there is also a ink department (one of the very few in Europe)where almost all of the super washable inks used for markers are prepared.
The plastic molding department is located on the ground floor of the plant and has 34 injection machines. From the raw material, in the form of granules of polyethylene, polypropylene and polyether which are die-cast and injected at high pressure inside a mould, the three plastic components that are used to compose a marker: the bottom, the cap and the tank.
To arrive at an increasingly sustainable product, Carioca is replacing plastic of fossil origin with second life plastic materials (coming from waste or industrial production scraps) including a new substance, which is called ecoalleneobtained from polylaminate milk and juice packages (such as tetrapack).
On the second floor there is the assembly and packaging department, which has 33 machines. The process is almost entirely robotic. Special electromechanical machines, equipped with control devices, through special funnels they load the plastic components into different tanks and transport them on belts, inside an automatic assembly line. Through the sensors of the machinery, the pieces are assembled and the tips and pads (purchased from subcontractors) are inserted.
The ink is also inserted: the company is one of the few in Italy to produce and use its own inks, which are mainly composed of water (95%) and food-grade dyes, to guarantee high levels of washability and safety, even for children. Preservatives are also added to the inks: in the right quantities, they guarantee the conservation of materials which during use – especially by children – can come into contact with microbes and bacteria. In these cases, a product without preservatives could be even more dangerous, deteriorate quickly and become a vehicle for infections.
The quality control laboratory is also located on the same floor of the factory, because production must comply with very strict standards. In the customization department they come the logos that distinguish the different types are applied of markers: this work is carried out by 9 screen printing machines, two printing machines and two sleevers. On the first floor of the factory, inside the assembly department, there are also semi-automatic packaging machines: with a conveyor belt, the markers are placed in the different packages in cardboard or PET (also second life). Carioca has adopted a sustainability policy which has led to the progressive elimination of the use of virgin plastic, both in terms of products and packaging.
Today, for example, fossil plastic in packaging is reduced by 95%. “Not only. We have also made the company more sustainable from an energy point of view, with the purchase of lower consumption machinery, the direct production of solar energy, the use of a purifier for the reuse of water”, explains Giorgio Bertolo, DG Carioca. “Thanks to’electricity produced with solar panels and purchased from certified renewable sources the emission of over 900 tons of CO2 was avoided. Our mission has always been clear: to design products that educate children to best develop their natural creativity.”
Source: Vanity Fair
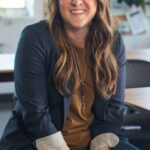
I’m Susan Karen, a professional writer and editor at World Stock Market. I specialize in Entertainment news, writing stories that keep readers informed on all the latest developments in the industry. With over five years of experience in creating engaging content and copywriting for various media outlets, I have grown to become an invaluable asset to any team.