One meal, even if it’s not business, can change everything. A year and a half ago, the Brazilian designer Silvana Catazine (Pernambuco, 1974) turned her head at one of the tables in l’Hortet, a charming restaurant in the Raval. “It had been a few weeks since I had just settled in Barcelona to attend a workshop in Elisava on biomaterials,” he recalls. Naifactory Lab, his design studio, specialized in ephemeral architecture for large events in Barcelona (such as Primavera Sound), Amsterdam, Paris, London and SÃ £ o Paulo, where he was in charge of decorating the booths of the carnival parties. Over time, the bleak landscape that the tons of garbage scattered around the streets depicted the next day led him to seriously rethink his work.
For the workshop’s final practice, Catazine had to craft an item from scrap. “I couldn’t think of anything, so I went to the Macba to get inspired.” The Eurekian answer came later, during lunch, and ended up on the appetizer plate directly in front of him. “It suddenly occurred to me that maybe the olive pits could be useful, so I took them away on a napkin.” Back home, he pounded them with a hammer into a thick mass. “The result looked good, so I contacted a few providers.” To his surprise, the Cordovan company Microlive agreed to send him a bag of bones for his experiment. “I was learning through trial and error until one day I realized that I had something very powerful on my hands.”
Her husband, the architect Joseán Vilar (Valencia, 1973), helped her to treat the new material with binders, plasticizers, colorants and waterproofing agents, all of natural origin, until he found the secret formula of the Reolivar patent, a biocomposite smart and 100% biodegradable. “The percentage is important because some plastics that are advertised as such in practice do not disintegrate”, adds Vilar, who acknowledges that the documentary The Story of Plastic by Deia Schlosberg (which provides unappealable data on the ineffectiveness of the recycling industry) changed his look and even his professional habits. “We use a residue from the oil industry to ecologically and sustainably close the cycle of an abundant by-product of the national economy.”
Bones and CO2
Spain represents the largest olive grove on the planet, with more than 300 million olives (the equivalent of an area of 2.5 million hectares) spread over 34 provinces in our geography. This business generates a whopping 450,000 tons of bones per year, the final destination of which is usually combustion as biomass. “Every kilo of bones that is burned emits two kilos of CO2 into the atmosphere, almost the same as a liter of gasoline,” says Vilar with the calculator in hand. “So Reolivar could become an important carbon dioxide sink in a few years. That is, we are not only talking about obtaining useful objects from biodegradable waste, but also about taking advantage of the Kinder egg that each olive contains to reduce the environmental impact “.
The mechanical behavior of this biocomposite is very similar to that of wood, which allows the milling or turning of the pieces and makes it especially suitable for the manufacture of furniture, decorative objects and ecological toys. The process is as simple as heating the residue to less than 100 degrees in a tank of water until it is melted. “You don’t need a lot of machinery, anyone can do it at home with a pot,” adds Catazine. “What makes the difference is the mixture with other ingredients and components that give it greater elasticity and resistance.” In their study-laboratory, Catazine and Vilar tested hundreds of combinations to obtain materials with the durability of wood (Reolivar tierra) and the lightness of blown glass (Reolivar aire).
The first Reolivar 3D prototypes, which had been developed in Poblenou thanks to the technology of the Remix El Barrio del Fab Lab program, captured all eyes at the last edition of the Marker Faire in Barcelona. “I think we were not aware of what we had discovered, because we set up our stand with all the humility in the world, without imagining that the collection of objects that we carry would generate such a stir”, Vilar is sincere. “We suspected that the novel olive residue could have many possible applications, but not that it would arouse much interest in visitors. It was as if they were proud that we had managed to extend the life expectancy of a genuinely Spanish material “. People were yelling “olive bones” and taking selfies.
‘Startup’
Last year they were selected for the XII edition of the Joya Barcelona fair and their Neomateria collection toured South Korea. These days several of his objects are exhibited at the CentroCentro space in Madrid, the Valencia Pavilion, the DesignHub in Barcelona and at the Etopia art and technology center in Zaragoza. In addition to stools, lamps, vases, toys and bowls (for maracas as famous as Danà © s Heveas and Köllen Design), they have received a commission from the NID-O studio to prototype a chair. “We designers have realized that the planet’s natural resources are on the verge of depletion and that the rhythms of consumer society are not compatible with our survival,” says Catazine. “That is why the sector is preparing for the big change.”
At the moment, Reolivar is in the startup phase (so they do not yet have billing figures) but its projection is unstoppable. Several business angels have been interested in this plastic substitute from waste that could have interesting applications in the cosmetic and food industries. “Another of our research areas has to do with containers and packaging”, confirms Vilar. “It is a field that requires a lot of specialization and a great investment, since the criteria for obtaining a certificate are very demanding. Each package reacts differently and the composition of the material must be adjusted to avoid migrations that interfere with the properties of the product. in question, whether it be a cream or a drink. ”
In a few months, when they complete the last stage of the incubation process at Barcelona Activa, they will launch the definitive brand, which will be linked to the values of the circular economy and the social workforce. The logo will not be in the shape of an olive, as they have already incorporated other superabundant residues into their laboratory about which they still cannot give details. “For us, the patent is not a form of enrichment, but a way of guaranteeing that the fruit of our research does not end up in the wrong hands”, explains the Brazilian designer. “Through our workshops we advise professionals who want to take an environmental turn to their business. We are very clear that our fiercest competitor is not within the sector, but outside, and responds to the name of climate change “.
Extra virgin wood
Before finding the alchemy hidden in the heart of olives, Silvana Catazine punctured the bone several times. “None of this would have been possible without the support and trust of the architect Anastasia Pistofidou”, confesses the Brazilian designer. “The Fab Lab in Barcelona put at my disposal all the necessary technology to develop my first prototype.” Without a 3D printer, a laser cutter, a number control milling machine, or a CNC lathe (like the one in the picture) it would all have been a fun wacko. Also in that laboratory, Joseán Vilar was able to experiment with the properties of one of the most abundant residues in Spain and undoubtedly the most unknown. “We discovered that the composition of the pit varies depending on when the olive is harvested,” reveals the architect. “If it is collected earlier, its color is lighter and its humidity percentage is lower.” Go ahead a clarification: all the black olives were green in their beginnings. What struck him most about this material (as old as it was pioneering) was its manageability. “It lends itself perfectly to machining, whether it’s cutting, sanding, drilling, turning, polishing or painting.” After preparing the mixture with the components, the resulting paste is poured into the molds for subsequent drying. “The advantage over other similar materials, such as wood, is that it adapts to any shape, allowing you to dream big.”

The plastic sea
From one of the windows of his studio in Vilasar de Dalt you can see the Mediterranean. From the other, the peaks of the Litoral mountain range. “We live and work in direct contact with nature”, celebrates Catazine, which was born in Olinda, one of the best preserved colonial cities in Brazil. “Olives are not styled there”, he jokes in perfect Spanish, “but coincidentally my second surname is Oliveira”. A little further north, on Pipa beach, the couple had a revealing experience a few years ago that encouraged them to return to Spain. “This area is very well isolated from the big cities and everything in it is paradisiacal: crystal clear waters, imposing cliffs and dolphins that come to the coast to eat. One day, suddenly, the beaches woke up covered in plastic. .. I couldn’t believe it. ”

For these two entrepreneurs, the pandemic has both warning (“last call”, they chant alimón) and opportunity (“first step towards a different reality”). During the months of confinement, they say, homes became a “sensory paradise” that forced us to rethink our place in the world. “Sustainable design is a rising value,” says Vilar. “People need to know that the objects around them are not damaging the planet.” That is why they trust their olive pits to help fill a new consciousness. “In this sense, we have set out to break the olive release record”, fantasizes Catazine. “Hopefully Reolivar goes so far as to become that grain of sand that precipitates a great change.”
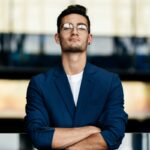
Donald-43Westbrook, a distinguished contributor at worldstockmarket, is celebrated for his exceptional prowess in article writing. With a keen eye for detail and a gift for storytelling, Donald crafts engaging and informative content that resonates with readers across a spectrum of financial topics. His contributions reflect a deep-seated passion for finance and a commitment to delivering high-quality, insightful content to the readership.