Almost 250 kilometers from the state capital, in São Carlos (SP), is the largest aircraft maintenance center in South America. Installed in a 95,000 square meter industrial park, Latam Mro serves, on average, 270 aircraft per year.
Mro is the acronym in English for Maintenance, Repair and Overhaul, which, in Portuguese, means “maintenance, repair and review”. Almost 70% of all the company’s scheduled maintenance in Latin America is done there, where nearly 2,000 people work.
The space, where the team of CNN He traveled at the company’s invitation, has the capacity to serve up to 16 planes at the same time. This number will increase later this year, as a new hangar is under construction and should be ready in the second half.
At the Latam Maintenance Center in São Carlos, preventive and corrective work on almost all models of the company’s fleet: Airbus A320 family planes and Boeings 767 and 787. The exception is Boeing 777, whose maintenance in Brazil is done in Guarulhos (SP).
The area also is licensed to provide services to Embraer and ATR aircraft – which are not part of the company’s fleet.
Engineer Marcos Melchiori, senior manager of Mro Latam, explains that, usually each plane is in the São Carlos complex for a period ranging from a week to 40 days. The length of permanence varies according to the complexity of the service performed.
Step by Step Review
According to Melchiori, when the aircraft arrives in São Carlos for review, the first step is the shortages of the tanks, so that the teams can work safely.
“The moment we enter the aircraft in the hangar, a process that we call the entry test. There are several systems of the aircraft that will be tested for us to identify if there is any fault. [revisão] Demand different disassembly, ”he explains.
Next, inspections are made: some visuals and others by the methodology known as NDT (non destructive testing – or non -destructive tests in Portuguese).
After performing the necessary services, when everything is completed, the aircraft begins to reassemble.
“The last step is the final tests, which is basically validating if the problems were corrected with the actions that were taken during the maintenance of the aircraft,” details Melchiori.
Repair
In addition to preventive maintenance, the complex also performs corrective repairs, ie repair when something unscheduled happens during a flight.
An example of this is the beak of an Airbus A320 that was destroyed on February 20 after shock with a bird during takeoff at Galeão airport in Rio de Janeiro.
The part of the aircraft that was damaged by the impact was taken to Latam Mro, where it was recovered and will be painted again. See how it was:

Workshops
In all, 22 workshops are part of South America’s largest aircraft maintenance center.
Meet some of them:
Landing trains
In the landing trains workshop, the equipment goes through cleaning, disassembly, inspection and galvanoplasty processes.
In galvanoplasty, landing trains are bathed in substances such as cadmium, copper and nickel. The purpose of this procedure is to provide protection to equipment, especially against corrosions.
Electronics
Through the electronics workshop, they pass aircraft communication systems, panels and popularly known components as “onboard computers”. One is the FMGC (Flight Management and Guidance Computer, in the translation of the acronym to Portuguese). Another equipment that passes by is the black box.
When components arrive at the electronics workshop, they are connected to equipment called ATEC, which “scan” all devices and points out possible flaws.
Emergency equipment
In the emergency equipment workshop, so -called escape slides are maintained – which are the inflatable slides used for the aircraft’s rapid landing.
The equipment is revised every three years. However, when they exceed 15 years of useful life, periodicity becomes annual.
During the review process, slides are inflated and are full for 12 hours. If, during this time, it is found that the pressure has dropped beyond the level considered acceptable, it is a sign that there is leakage.

Thermoplastics
In this sector, all plastic items used in the aircraft cabin are manufactured.
See some of the items produced in the thermoplastic workshop:
- Feeding trays
- Chair coating
- Window frames
- Sanitary seats
- Armchair arms

Tapestry
All fabric items are produced in this workshop, such as carpets, curtains and armchair covers.
The upholstery of the armchairs is also assembled in this place. Still on the armchairs, the company reports that they are exchanged every 36 months.
Already the covers of the armchairs are washed whenever there is need. They can wash at most at most 25 times. Then they have to be discarded.
Mechanical school
In addition to the workshops, the LATAM Maintenance Center in São Carlos has a school for aviation mechanics. The space was inaugurated in December last year and the first class began classes in January this year.
LATAM says it is the only Brazilian airline to have an instruction center certified by ANAC (National Civil Aviation Agency) for the formation of aeronautical maintenance mechanics. The vocational course lasts 18 months.
For students’ learning, parts of aircraft are available through the school area, where participants can perform practical tasks. There are engines, propellers, pieces of fuselage and aircraft models.
Outside, the cabin of an Airbus A320 has been dismantled so that students can understand and visualize how each component of the interior of the jet works. There is also a wing of the same aircraft, which was opened at some points to enable access to the fuel tank. See below :
This content was originally published in SP has the largest aircraft maintenance center in South America; Meet on the CNN Brazil website.
Source: CNN Brasil
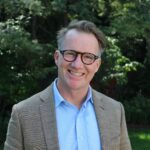
I’m James Harper, a highly experienced and accomplished news writer for World Stock Market. I have been writing in the Politics section of the website for over five years, providing readers with up-to-date and insightful information about current events in politics. My work is widely read and respected by many industry professionals as well as laymen.