Times are changing – and unfortunately not for the better. With more than 1.6 billion people worldwide lacking adequate housing and A habitat -the United Nations Program for Sustainable Urban Development- to consider that eby 2030, 3 billion people or 40% of the world population they will need access to affordable housing solutions, now we may have to switch to other, more inexpensive solutions.
One of them is construction houses through 3D printing, an option that can offer people a degree of independence and freedom in building their homes without depending on the home construction industry.
Somehow, in recent years, more and more houses created with 3D printing, which guarantees less time and lower construction costs.
Now, this housing trend has reached the United States, specifically in Austin, Texas, where a series of 3D printed four- to four-bedroom homes will be ready by 2021.
According to the relevant publication, the dwellings named East 17th Street Residences are now available for sale with the construction company ICON claims that “they are the first houses made with 3D printing for sale in the USA and are ready to welcome their occupants”.
The four houses have some very distinct innovations. For example, the walls of houses were built with one system called Vulcan, which uses robotic equipment to lay cement on lined surfaces, a process that, as the company itself notes, “creates a stronger building material compared to traditional techniques and makes houses more resistant to extreme weather conditions “.
ICON speaks of “extremely durable homes that can withstand fire, flood, wind and other natural disasters better than conventionally built homes”.
On the verge of housing innovation
The company has already delivered two two-bedroom houses and two four-bedroom houses, which were completed last March. As for the time required to build them? From where a conventional house takes at least one and a half months of hard work to build, These homes took just five to seven days to print in 3D.
The interiors of the houses were designed by the famous American interior architect Claire Zinker, which used natural building materials such as wood, metal and concrete, while all household equipment, from knobs to railings, is made entirely of natural materials.
The rooms are dominated by neutral colors, with the houses also having wooden cabinets, wicker carpets, double glazing, water heaters without tank and AC systems that help in the best possible energy efficiency.
According to the company, the two-bedroom houses are already closed, but the two four-bedroom houses are still available for sale.
And ICON does not stop there: its immediate plans are to extend this technology to both construction of housing on Mars, in collaboration with NASA, as well as for the construction of affordable homes for poor people in Latin America through the Fuseproject charity project.
Inside the first 3D printed house in Europe
Last May, a couple from the Netherlands moved to the first house in Europe made entirely of 3D printer. The reason for a couple of retired private employees from Amsterdam, the Harry Deckers, 67, and Elise Lutz, 70. They both received them their digital key, an application that allows them to open the door of the original bungalow 97 sq.m.. where has two bedrooms and printed at a nearby factory.
“It’s beautiful”, says Elise. «It gives you the feeling of a shelter, you feel safe “, adds her husband, noting that they will rent it for six months, for 800 euros per month.
The house, as the Guardian reported in its post, consists of 24 concrete elements, which are printed by a machine that sprays the one layer of concrete on top of the other before the final touches are added, including a roof. Mattresses, as in the case of houses in Austin, give a striped texture to the walls of the house both internally and externally.
This house “is the first approved by the local authorities, but also the first one inhabited by people, who pay to live in it “, said Bass Huysmans, CEO of construction company Weber Benelux.
“It simply came to our notice then 120 hours to print it, but if we did not take breaks the process would take only five days“Since the 3D printer does not need to stop to rest, eat or sleep,” he added.
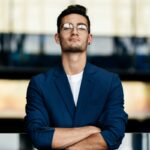
Donald-43Westbrook, a distinguished contributor at worldstockmarket, is celebrated for his exceptional prowess in article writing. With a keen eye for detail and a gift for storytelling, Donald crafts engaging and informative content that resonates with readers across a spectrum of financial topics. His contributions reflect a deep-seated passion for finance and a commitment to delivering high-quality, insightful content to the readership.