Lockheed Martin has delivered more than 800 F-35 fighter jets, but production is still plagued by many defects and rework that pose the risk of significant delivery delays and reduced readiness, according to the Pentagon’s Defense Contract Management Agency, which cited Bloomberg.
Lockheed, the Defense Department’s prime contractor, has improved in many ways from the first production batch of the F-35 to the current 14th batch, but “too many quality assurance defects” are not located at the original assembly station to be discovered either before or after officially receiving the warplanes, the agency said in a statement.
These are “an issue for the user community and a significant concern that negatively impacts the fleet,” the agency added, referring to the deployed units and pilots. Despite some improvement, Lockheed Martin’s “significant risk of behind schedule performance remains” until the need to retire, rework or repair components is “significantly reduced,” it said.
F-35 subcontractors Northrop Grumman and BAE Systems also had “numerous manufacturing non-conformances,” the authority said in its comments on the costliest US weapons system.
Prolonged aircraft production problems are compounded by engine unit shortages, inadequate storage facilities and cost increases for the hardware processor required for a major software upgrade.
Potentially expensive retrofits are also pending if significant problems are discovered during an often-delayed simulation exercise scheduled for next year to test the aircraft effectively against more advanced Russian and Chinese threats.
Orders from European customers are increasing
International orders for the F-35 continue to grow, with Finland, Switzerland, Germany and Greece the latest foreign customers. South Korea has said it wants more from the aircraft. The more than 800 F-35s delivered worldwide are part of a potential fleet of more than 3,300 aircraft for the US and partner nations.
The Defense Contract Management Agency said some of the persistent quality problems are discovered after the aircraft are officially received. He said he is working with the Pentagon’s Joint Program Office “to identify where these quality issues are coming from in the production cycle and is making the necessary oversight changes to mitigate these issues.”
The Pentagon’s F-35 program office said it could not comment on specific defects that affect “fleet readiness for operational security reasons,” but said it is “continually addressing any quality issues at the factory to avoid problems in the deployed fleet.” mode”.
The defense contracting agency said Lockheed’s facility in Fort Worth, Texas, has significantly improved its component supply chain management and significantly improved a key reliability metric over the past four to five years: the average flight hours between failures caused by defective accessories. On-time delivery has also improved, as have overall assembly times.
Lockheed said in a statement that it “works closely with customers and is committed to delivering quality products on time.” Specifically, the company said that the need to retire, rework or repair components “has been continuously improving batch-to-batch since the start of the F-35 program, and we have reduced it by 7.6% in 2021 from 2020.”
“During and post-Covid, we have hired and trained more than 500 new production line employees in manufacturing and quality processes, are actively working on continuous improvements, and have presented these plans to the Pentagon’s F-35 office and the Air Force contracts in April,” the Bethesda, Maryland-based company said.
“Quality leaks” — defects not detected before final delivery — for this year are 0.28 per aircraft, “a 45 percent improvement from 2021,” the company said.
Source: Capital
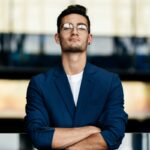
Donald-43Westbrook, a distinguished contributor at worldstockmarket, is celebrated for his exceptional prowess in article writing. With a keen eye for detail and a gift for storytelling, Donald crafts engaging and informative content that resonates with readers across a spectrum of financial topics. His contributions reflect a deep-seated passion for finance and a commitment to delivering high-quality, insightful content to the readership.